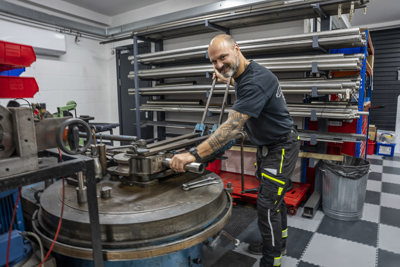
The Salford engineering firm has unlocked future growth opportunities using Made Smarter advice and support to help them create a digital transformation road map.
Atec Engineering Solutions designs, manufactures and repairs complex electronic and electro-mechanical equipment used in the aerospace, defence, nuclear, and oil and gas sectors.
But business growth was being hampered by flawed and disparate IT and data processing systems, as well as a culture of resistance from its 42-strong workforce to move away from traditional ways of doing things.
It prompted Atec to engage with Made Smarter’s digital transformation workshop, which helps manufacturers maximise productivity and return on investment by improving their readiness to adopt the right digital technologies.
View the Case StudyThis roadmapping process helped map our IT systems, show how disjointed they are and how to make a big difference with small changes. Now we are in a position where we are ready to adopt the right digital technologies.
Andrea Hough, Managing Director of Atec Engineering Solutions
From its 22,000 sq ft site in Salford, Atec uses an MRP/ERP system to manage product workflow and labour requirements for a job, starting when an order comes in until when it is delivered to the customer.
But the £7m turnover business has been puzzled by its inability to improve performance to make and repair its own product range, which in turn was stifling its capacity to manufacture third party products, a huge growth area.
The problem came down to the fact different departments were not closing off jobs consistently or using the ERP system effectively.
It meant that department heads had to create workarounds to rectify issues with performance reports.
“The data going into the system was wrong, but there was a reluctance to acknowledge that,” Andrea explained. “Instead they implemented satellite systems rather than correcting the data. It meant that we were missing delivery deadlines, not understanding why and not being able to improve.”
Atec was also struggling to reduce the amount of time it was taking to quote for its own products because the data sat in different departments, not centrally.
The digital transformation workshop involved an initial online digital readiness assessment, two half‐day workshops with a specialist adviser and a post‐workshop debrief.
The aim of the exercise was to highlight how the adoption of digital technologies can benefit the business, identify which digital technologies are most appropriate to invest in and outline the business case for investment.
Andrea said: "Using someone from outside the business, who was willing to ask the obvious questions, enabled us to sit around a table and look at the problem with fresh eyes.
“That first session was a way of laying it all out in front of us then taking a step back to ask ourselves the pertinent question: what are we trying to do here? Then we were able to able to pinpoint the things that were getting in our way.”
The process showed Atec that data integrity was the first but major step towards solving its problems and creating a pathway to new growth. This involved correcting and centralising data.
“We needed a data cleanse, so I created the mantra that ERP was king. We had to trust the data coming off it or go back and correct what was wrong, Andrea added. “But some people were entrenched with the traditional ways, so we had to focus on changing the culture, changing attitudes and getting them to look at the bigger picture.”
The results of correcting the data were immediate. Performance reports which showed that only 50% of jobs were being completed on time, suddenly shot up to 80%.
“Once we had corrected that data it felt like an overnight improvement,” Andrea said. “That gave a huge boost to morale and was a lightbulb moment for those who were entrenched in their old ways.”
With clean data Atec has been able to focus on improvements.
“Now we can trust the data it becomes central to all decision making and the real work has started to get from 80 to 97%. Our work now is about improving performance through processes.”
The on-going process of centralising the data has seen the time it takes to quote for Atec’s own products fall from an average of four weeks to three weeks – a 25% decrease. The aim is to bring that down to a 48-hour turnaround.
Andrea said none of the above would have been achieved without the roadmapping exercise.
“Giving ourselves the headspace to complete the workshop helped us realise what opportunities there are to improve,” she said. “It was an easy first, practical step – and has had a huge impact on the business.”
Atec is also progressing two other IT projects: a Smart shop floor to eliminate paper; and a new digital visitor system.
It is also looking at ways of integrating data from the supply chain to its own systems to grow its build-to-print business.
“Our growth strategy is to expand our offering of 'build to print' products so we need to adapt our systems,” Andrea said. “There are real opportunities out there, and now we are on the way to reaching them.”