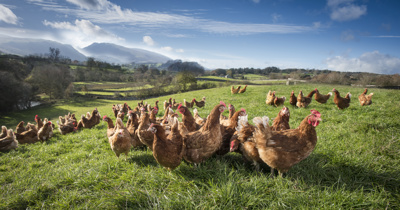
A free-range egg farmer in Cumbria has invested in a ground-breaking digital solution using sensors, big data and analytics to produce more eggs and improve bird welfare.
Bell Mount Farming, in Penrith, has 60,000 chickens producing 1.5M eggs per year for The Lakes Free Range Eggs group, which supplies Sainsbury's, Tesco and McDonald’s. Run by passionate animal welfare-advocates David and Helen Brass, their free-range chickens enjoy the run of 25 acres of woodland. Despite these conditions, the Bell Mount, like the whole industry, has been unable to improve mortality rates among its flocks.
Using match-funding through Made Smarter, Bell Mount is pioneering a bespoke hardware and software solution which uses sensors and data analysis to try and create and maintain the optimum conditions for egg production and hen welfare.
View the Case StudyI’m a junkie for data. It has always been there, but this is the first time we have been able to get so much of it, live, and with the capacity to analyse.
David Brass, Co-Owner of Bell Mount Farming
There is an accepted truth in the free-range egg industry that the better the welfare conditions for a chicken, the longer it will live, and the more it will produce. But despite this, producers have struggled to find a solution to reduce the number of chickens which die prematurely which is around 8%.
David Brass has spent decades working with industry leaders, scientists and academics to develop ways to overcome these problems.
“Genetically, the chickens used in our industry have been pushed to the limit, so the smallest human error - like leaving the lights on for too long, or the feed or water distribution not working properly for a few hours – or a disease challenge, can result in significant problems,” David explained. “A lost egg here and a lost egg there over the lifetime of a flock really adds up, and at the sharp end you’re looking at deaths, which can be significant numbers. Farmers and producers simply cannot stay on top of those problems 24-hours a day. And then it can be too late.”
The answer to this conundrum has been focussed on finding a way of monitoring the chickens around the clock, producing reliable and meaningful data, and then analysing it to achieve its aims. The Bird Box free-range egg management system aims to do just that. The bespoke solution involves a control cabinet linked to electric and water meters, feed weigh cells and an environmental sensor array in the shed.
Feed, light and the ventilation data is collected from sensors, along with monitoring information such as bird health and performance from the producer.
The data is transmitted in real time and store on the cloud where it is analysed and displayed on a web and app platform. This is accessible to the supply chain which includes the producer, egg packer and veterinarian and accessible in real-time. It also produces early warning alerts to the farmer if any urgent action is needed to keep the optimum conditions.
“At present, there is no real time data collection system in place across the UK laying flock to monitor egg laying hens,” David said. “This system alerts any changes in the conditions, such as a water leak, too much light. It really aims to nip problems in the bud and get rid of human error. Made Smarter has been a godsend. The match-funding has enabled our ambitions to invest in the system which has been developed to help producers make better, evidence based, management decisions which would help the whole supply chain become more efficient and improve bird welfare.”
Bell Mount installed Bird Box in August, so data analysis has just started. But initial findings show that has forecast egg production and mortality rates in-line with trials which saw increases of 12 more eggs per bird and a 2% reduction fall in deaths.
David said: “We knew the system would work, and now we are showing that it does.
“Across a flock of 16,000 birds, that equates to profit increases of around £16,000. If you look at the whole of the UK laying industry, a reduction of 2% equates to about 500,000 birds – a significant sum. Then there’s the savings you make with energy, using less electricity and water. It costs you less to produce more eggs.”
Since demonstrating the technology and the benefits, other farms have started to explore adoption. David is confident the bigger performance benefits will come as more data is collected and analysed, and when more egg producers get on-board and link to the system.
“Once more and more farms sign up, you will also be able to compare how you’re getting on with others, which could identify problems you need to resolve. Most of these farms are simple livestock operations, so this is a big jump for them. For some it’s the shock of the new technology. But once they see how easy it is to use, the benefits, it becomes a no-brainer.” David said.
The software also has the capacity to link with academic studies working on research into hen welfare. The forecasted increase in the region’s GVA increase over the next three years is £309,391.
David is excited about the potential use of this new data.
“I’m a junkie for data,” he said. “It has always been there, but this is the first time we have been able to get so much of it, live, with the capacity to analyse. It’s from there we can find the efficiencies. We’ll be able to see whose flock performs the best and work out why, and then replicate that across the industry. The potential is amazing.”
In the future the data collected to monitor flocks enables further Big Data opportunities and academic uses, including behaviour or trend identification, and early detection of disease.
“There are a whole stack of scientists itching to get their hands on that data. It is so valuable. We really have taken the first step in the collection of a unique data set that will be shared by industry stakeholders, improve performance, welfare and aid research into the industry’s most pressing problems.”