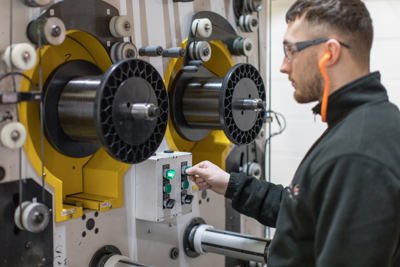
A manufacturer of advanced materials, supported by Made Smarter, has taken a transformative step after adopting digital technology to capture, analyse and manage production data.
Bindatex, based in Bolton, has developed a niche market providing a precision slitting service into high-value manufacturing industries, such as aerospace.
With new opportunities on the horizon, the business recognised it needed to improve how it monitors production to increase capacity and provide high service levels.
Using Made Smarter’s digital transformation workshop to identify its challenges and potential solutions, Bindatex adopted Total Control Pro (TCP), a cloud-based production data capture system that enabled the business to track products through the manufacturing process.
Applying the solution to its critical narrow slitting line, Bindatex saw productivity improve by 20%. Unplanned overtime was eliminated, lead times reduced and on-time delivery performance improved.
New capacity also gave Bindatex greater agility which meant they were able to reconfigure production to die-cut discs for filters used in ventilators for the NHS, and respond rapidly to new business opportunities.
View the case studyOur partnership with Made Smarter has been transformational. We developed a digital strategy and have invested in technology which has given us better control of our manufacturing. Made Smarter has had a cultural impact on the business. The apprehension has been taken out of digital technology and got everyone enthused and excited about the future.
Chris Lever, Managing Director of Bindatex
Formed in 2004 to service the traditional world of bookbinding and printing, Bindatex developed expertise in cutting difficult to handle materials and has diversified into the composite sector.
Opportunities to be part of the supply chain for major aerospace programmes for Boeing, Airbus and SpaceX was the driver for Bindatex to resolve the issues it had with limited data visibility and control.
The digital transformation workshop identified a major challenge with its manual and time-consuming system which relied on paper-based data capture and spreadsheet analysis.
Chris explained: “Our manual approach to capturing production data meant our planning wasn’t efficient, and due to our success with growing the business we needed better data to help achieve our planned increases in capacity, sales, delivery times and customer satisfaction. “We knew we had to change, so we turned to Made Smarter for its expertise.”
Total Control Pro has enabled more efficient tracking of each order through its entire manufacturing process.
When a sales order comes in it is given a unique identifier that is associated with a barcode on a batch. As the product moves through the manufacturing process it is scanned by operators.
The system then provides productivity reports by product, batch, machine, and operator, giving the management team the ability to analyse the time orders are taking and make process improvements based on reliable real-time data.
Armed with data showing exactly how long it takes to make a product, Bindatex’s production planning and scheduling capability was instantly transformed.
When the new solution was applied to its critical narrow slitting line, Bindatex reduced unplanned stoppages and downtime. The whole cycle time reduced from 4.5 hours to 3.5 - a productivity increase of almost 30%.
By rolling the solution out across the entire factory, Bindatex estimates that it could increase overall productivity by 20%.
With new capacity planning Bindatex has reduced lead time by an average of 25% and is able to deliver all orders on time.
It estimates that greater efficiency in the energy used to power its factory and machines could reduce its carbon emissions by 20%.
“With oversight and control, backed up by data, we can do more with what we have got and respond quickly to opportunities,” Chris said.
“When coronavirus and lockdown began to impact, we were able to plan more effectively and sustain aerospace orders and respond to other opportunities. When the government’s ventilator call came, we were able to react. When furniture retailers were looking for protective covers for infection control, we were able to pivot, manufacture, and deliver very swiftly.”
Bindatex is now able to provide a high capacity, credible composite slitting capability to bolster an entire UK supply chain and create export opportunities with European customers. It estimates export sales to Europe will increase by up to 20% over the next two years.
As well as aerospace, other potential growth areas include automotive, oil and gas, and consumer sectors.
The adoption of this new technology is a vital step on Bindatex’s digital journey towards an entire digital factory while ensuring high value manufacturing capability remains in the North West.
The next step is a digitally controlled, inline automated slitting and spooling line that uses Artificial Intelligence to monitor quality.
“Customers now see us as a progressive brand, dynamic and consultative, rather than a commission manufacturer,” Chris said. “Made Smarter has catapulted our business to a new level.”