Blends uses various basic software to process data for sales and purchases, generate quotes and invoices, and process recipes and orders.
It is also reliant on spreadsheets to monitor and process new product development, meaning the business is too slow to react to opportunities.
Meanwhile, data used in the technical and quality control systems is processed manually, which is time consuming and prone to duplication and error.
Michael said while functional, none of the software solutions communicate with each other.
“We’ve been growing the business gradually to ensure reliable service to our customers and not overselling our capabilities,” he explained. “But we are walking around with scraps of paper recording information and typing it into spreadsheets.
“We’re now at a crucial point when we need to eliminate those flaws and become more streamlined and efficient. We need the software to do much more - and quicker.”
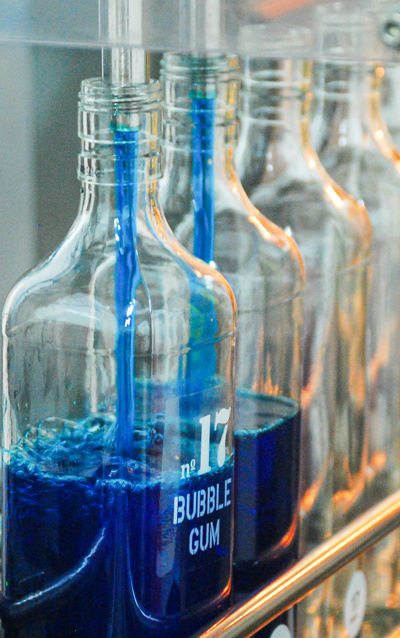
Over the last 21 years, Liverpool-based Blends Holdings has established itself as one of the UK’s leading manufacturers of specialist food ingredients.
Through innovation and diversification, the family run business has developed four strands: commodity food ingredients such as glycerine and glucose; food flavours; food colourings; and co-packing for big names like Dr. Oetker, Revolution Bar Group, Aldi and Lidl.
In the last two years Blends has doubled its manufacturing facilities on Knowsley Business Park to 70,000 sq ft and has plans for a new £500,000 extension to accommodate its 60 staff. Turnover has also doubled to £23M and the future looks even brighter.
But the family business – run by Mike and Ann Rowark and their sons Michael and Phillip – recognise the major barrier to growth is its reliance on outdated, paper-based systems.
It has set its sights on adopting Industry 4.0 technologies to make it more efficient and boost productivity.
The cloud based solution will enable real-time and remote analytics and monitoring by the management and executive team. This first step into digitalisation is going to make a significant difference to our entire operation.
Michael Rowark, Operations Director of Blends Holdings