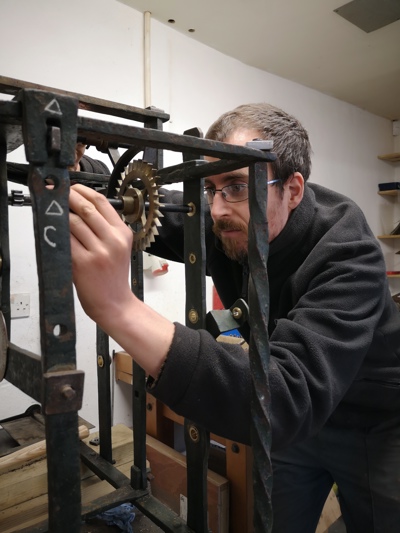
A Cumbrian clock repair and restoration specialist is bringing conservation and horology into the 21st century using digital technology adopted with Made Smarter advice and support.
The Cumbria Clock Company is responsible for the maintenance of more than 1,000 church and public clocks in the UK including some of the most prestigious timepieces. But the company has long outgrown its out-dated, paper-based maintenance monitoring system.
Download their story (PDF)Made Smarter has not only accelerated our growth, but opened our eyes to so many possibilities which could transform our business from reactive and regular service and repair to a proactive data-driven service provider.
Keith Scobie-Youngs, Director of The Cumbria Clock Company
Established by Keith and Lynn Scobie-Youngs 30 years ago, CCC’s team of 18 includes engineers who travel 260,000 miles per year on a maintenance schedule and conservators who carry out repairs from the Penrith workshop.
The work schedule is managed using a mixture of paper files, spreadsheets and magnetic whiteboards.
“Over the last 30 years our system has evolved to cope with our increase of clients,” Keith said. “But it is becoming too unwieldy for an analogue system and we need to find a better way to do things.
“Our lack of overview of the location of all our clocks and our engineers means that opportunities to be more efficient with our service routes are missed. That means driving past a problem clock by mistake and then having to return. That’s extra time, cost and mileage.
“We’ve also had problems with communicating the full and correct information to our engineers, which have led to errors, unnecessary delays and wasted journeys.”
A bespoke digital management system with desktop and mobile app will give the business access to a complete history of each clock, parts and costings, maintenance schedule, technical documents and photographs.
Engineers will access the app on a tablet to view their schedule of jobs and routes, contact details and any health and safety concerns they need to be aware of. They can then capture and upload information and photographs in real-time, and order new parts.
Meanwhile, a dashboard and interactive map will give management an overview of all clocks, job types and status, and engineer schedules.
Cumbria Clock Company believes the solution will significantly improve its efficiency to plan routes and combine service visits with call backs and inspections, and reduce its annual mileage by 30,000. This would not only save a significant sum of money, but reduce its emissions by 11%, the equivalent to 12 tonnes of carbon.
Keith said: “My vision of the system is to be able to see an interactive digital map giving us a complete overview of all our clocks and engineers, which will enable us to plan our work more efficiently.
“This system will vastly improve how we do things, increase profit, give us more scope to create new jobs, and reduce our carbon footprint, which is something very important to Lynn and I.”
The app will allow the engineer to capture, store and upload vital data, which will save time and reduce the number of visits they need to make to the site.
“This solution will give engineers all the correct information about the clock, its location and its history, at their fingertips,” Keith added. “Instead of us waiting until the end of the day for an engineer to send us some paperwork or an email, the information is in the system immediately, so we can act.”
At the end of the process Cumbria Clock Company can produce a comprehensive conservation report for the customer, at the touch of a button.
Cumbria Clock Company is also exploring a digital chip tracking system which will enable the business to remotely monitor clock functions, such as time keeping, strike and chime sequence, and power outages, to better understand problems before the engineer attends onsite.
Data captured from these clocks could then be used to create a digital twin, a virtual replica of the clock, for the purpose of writing operations and maintenance manuals.
“At our heart we are conservationists finding engineering solutions to keep some of the UK’s most precious clocks running,” Keith said. “What we try and do is combine the old mechanical world with modern technology. We need to embrace the opportunities it offers our business.”