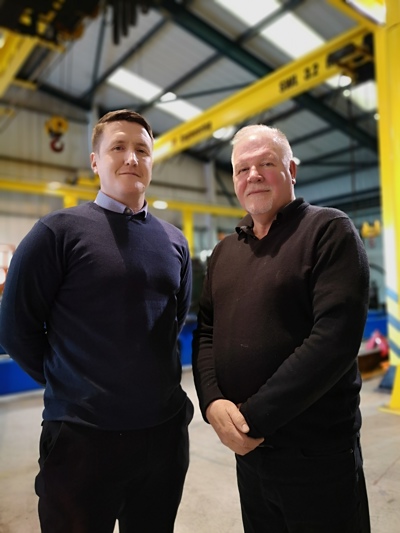
Based in Widnes, Cheshire, the company has developed in-house expertise in steel fabrication, mechanical engineering, welding, hydraulics and electrics, and boasts leading clients in the manufacturing, maritime, automotive and construction sectors.
DT Engineering recognises that in order to grow, it needs to diversify and embrace industrial digital technologies (IDT).
View the Case StudyAt its heart this is a system which makes health and safety the boss by preventing the mis-use of potentially dangerous machinery by unauthorised or untrained personnel.
Tom Coyle, Managing Director of DT Engineering
The company is often asked to provide lifting solutions which fit the customers’ needs and production requirements, but also have an absolute focus on safety.
DT Engineering believes it is a common oversight across industry to allow untrained and uncertified personnel to use lifting equipment and cranes, and there are too many ways to circumnavigate procedures designed to ensure the safe operation of potentially dangerous equipment.
The company believes there needs to be a stronger set of controls for authorised staff and competent, trained personnel, to gain access to potentially lethal lifting machinery.
DT Engineering is developing a ground-breaking smart access system for industrial machinery to allow or deny access to it through a set of user-friendly operator interface modules.
The system connects a machine’s control systems with a secure cloud-hosted database, sophisticated interrogation software and a web portal for system administration.
It means whenever someone wants to use the machine, their access using an RFID or biometrics is scrutinised for authorisation.
The system records all human interaction with the access panel and machine in a live, real time reporting environment.
It also prompts management when a user requires refresher training or recertification in their competence to operate specific machinery.
For the past two years DT Engineering has been developing the smart access system architecture with the Manufacturing Technology Centre, part the High Value Manufacturing Catapult, supported by Innovate UK, the UK’s innovation agency.
Now, through a successful application to Made Smarter, DT Engineering can now pursue the technology solution for its design.
Tom Coyle, Managing Director, said: “In heavy industry production is king. Businesses are under pressure to get jobs done at all costs. Add archaic attitudes regarding health and safety, and you have the potential for catastrophe. We think that by bringing machines and IDT together we can eradicate accidents and save lives.”
Although at prototype stage, DT Engineering hopes that the system that may subsequently be productised and sold into global markets for use at all levels of plant and across all sectors.
Adoption in the UK, and exports, could see an almost 50 per cent increase of staff over the next three years.
The proposals will also see a benefit to the region, with GVA expected to increase to £320,230 by 2022.
Tom added: “Success of this project will completely transform our business, allowing the company to grow and become far more profitable as we anticipate the integration of digital technologies and systems to complement our current core business.”
DT Engineering has also identified the potential of using virtual reality as part of the installation process after it has been exported.