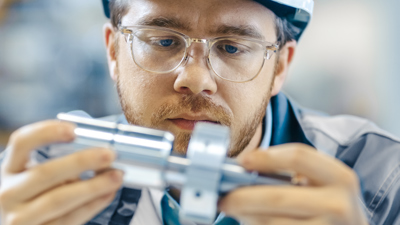
A manufacturer of specialist components for aerospace, power and automotive sectors is forecasting a 10% productivity boost after introducing a bespoke machine condition monitoring solution, supported by Made Smarter.
ELE Advanced Technologies (ELE), based in Colne, uses high-tech engineering technology, including advanced robotics to make hot end gas path components such as turbine blades, nozzle guide vanes, and ring / seal segments from exotic metals and nickel-based alloys like Inconel and Nimonic.
To preserve its exceptional customer service is dependent upon having a predictable process capability and reliability, as well as reduced machine downtime through unplanned reactive maintenance.
View the case studyThis investment is a huge step forward for our business. It will ensure ELE remains competitive and continues with its growth strategy to double revenue and increase its manufacturing footprint. We would never have gone down this path without Made Smarter. We were given the right, impartial advice, support, and connections from the start. Made Smarter’s approach has helped us commit to the project and deliver it despite the market uncertainty. This project is very much seen as one of the tools that will help us overcome the current challenges relating to Covid-19 and Brexit.
Dave Dudley , Technical Director
To overcome this challenge ELE has adopted a bespoke machine condition monitoring solution which uses data collection and analysis to predict issues. It then automatically notifies the supervisor or maintenance team in advance of any major machine malfunction and lost production.
The solution then automatically records information such as fault analysis, actual downtime or time lost, to give more meaningful and accurate information to management. This allows them to make real-time informed decisions to prevent the fault developing and reduce downtime by sourcing critical spares earlier.
ELE forecasts that the technology will improve key machine uptime by 10%, reduce maintenance spend by 10%, and improve accuracy and reliability by 10%. It will also create an additional new role in the maintenance team and upskill four members of the current workforce.
From a business supplying compressor blades in the 1950’s ELE has evolved to manufacture products for blue chip customers in the power generation, aerospace and automotive sectors.
In recent years, digitalisation has been high on ELE’s agenda, and it has been investing in its future, spending £7m on new machinery and new digital tools during the pandemic. However, currently, most machines are operated manually and not managed by a digital system.
This means when the process varies due to machine issues, the operator can easily miss the moment when the parameter tolerance levels are exceeded.
This also means little is known of machine performance and product quality until the cycle is finished and end of shift bookings are made.
While the machines are serviced regularly, performance issues and mini breakages happen. However, the lack of data means root-cause analysis relies on people and their account of events which is not always reliable and not sustainable with growing production demand.
Dave explained: “When a machine breaks down, we diagnose the problem and fix it. But that reactive approach to maintenance has its problems. Some replacement parts take a long time to source or can even be obsolete. This leaves us in a challenging position as it can take down an entire cell for an unacceptable period or means we have to carry a large inventory of critical spares.”
“The reality is that with unplanned maintenance, more often than not there is never enough time for identifying the root cause. As a result, a sticking plaster may be applied to have the machine operational quickly.”
“What we needed to develop was an early warning signal to highlight when machines are no longer performing at their optimum level, so we could investigate any issues while the machine was still running.”
By working with Made Smarter, ELE has adopted a machine condition monitoring solution.
Sensors have been fitted to six business critical machines to record a variety of signals such as spindle load, coolant pressure, temperature, and motor load.
These signals are fed into a control box where they produce a baseline for optimum machine performance for each part number produced.
A dashboard on the machine displays real time measurements, giving the operator a quick visual of performance.
If the performance starts to deviate the dashboard will display a warning light enabling the operator to assess the situation and potentially escalate to the maintenance engineers.
The engineer is then able to perform diagnostics and analyse any trends, putting the wheels in motion to repair or replace a required part before the machine breaks down.
Data captured from the machine is available on demand to production supervisors to perform any further analysis and diagnostics.
An example would be coolant pressure where a known pressure per square inch (PSI) is required but varies during the cutting cycle. The data sensors would establish what is the norm, and where pressure drop offs occur away from norm, this would help identify potential blockages or pump failures.
By introducing machine condition monitoring ELE will achieve a level of data management which will improve machine uptime and accuracy and identify efficiencies.
The key benefits anticipated are an increase in productivity, significant reduction in maintenance spend and much improved OEE, and increased customer satisfaction through reduced disruptions to delivery.
The project will also have a positive impact on the safety of their manufacturing process and will help reduce energy consumption.
The company is committed to rolling out the project to all their key equipment in the future and connecting it to the same platform. Any investment in new machines will have this technology built in or bolted on at supply stage.
The integrated approach will be central to its plans to move to a larger factory in Nelson in 2022.