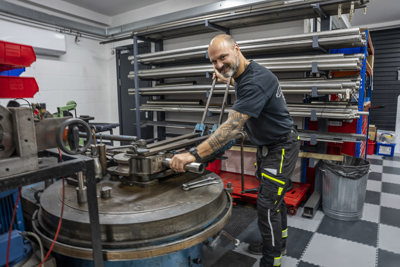
A manufacturer of high-quality motorcycle exhausts is unlocking its capacity to innovate and grow using an integrated digital design solution, with the support of Made Smarter.
Fuel Exhausts, based in Kendal, is investing in a 3D scanner to capture digital versions of parts and components, 3D CAD software, and a 3D printer for producing prototypes of end caps and parts for exhausts.
The technology will enable the business to design and test product ideas in virtual reality before manufacturing them.
It will radically change the way the business operates, making the prototyping process 14 times quicker, increasing productivity, eliminating waste, reducing costs, and increasing profitability.
Meanwhile, 3D scanning technology will introduce reverse engineering of parts into the business, opening new markets.
View the Case StudyWe are a small but very dedicated team who strive to provide a fantastic product with second to none customer service.
Over the two decades we have been trading, digital technology has moved to the forefront in many areas of manufacturing, with the support of Made Smarter we are ready to embrace the opportunity it offers to manufacture prototype parts and new products in-house and move into other areas of production for parts and accessories to complement our current range of exhausts.
Damian Turner, Co-owner of Fuel Exhausts
Fuel Exhausts produce parts for motorcycle exhausts to specific design requirements.
From forming everything by hand 21 years ago Fuel Exhausts has incrementally invested in digital technology to improve speed and accuracy.
Fuel Exhausts now wants to apply new technologies into its manufacturing to make its processes more efficient, increase profit, and capture a larger market share.
Damian explained: “Our prototyping process can be time-consuming, expensive, inefficient, and carries the risk of occasional human error.
“For instance, we use old school engineering skills to make a prototype by hand, draw it on CAD software and outsource manufacture to a company which uses automated CNC processes. It can then take up to 10 days for that prototype to be shipped to us, and from time to time, the end result can be millimeters out, meaning we have to scrap it and start again.
“It is this waste of time, money, resources and material we want to tackle.”
With the support of Made Smarter, Fuel is investing in an integrated digital design solution, which includes a 3D scanner, 3D CAD software, and a 3D printer, supplemented by a high-powered PC and a digital camera.
The scanner will capture the detailed dimensions of the motorbike and link to 3D CAD software and using photogrammetry, extract 3D information from the photographs, and create a 3D model.
Fuel Exhausts will then be able to use the 3D printer to produce prototype parts onsite.
The adoption of additive manufacturing will transform the prototyping process, ensuring a right-first-time approach.
It will grossly reduce the time spent manufacturing and revising the initial prototype, from 14 days down to 1 day.
This project will reduce wasted time, wasted resources, and environmental impact by eliminating the need to use external suppliers for prototype parts, which have associated travel, shipping and energy costs, and make the business more profitable and productive.
The 3D scanning technology will allow Fuel Exhausts to scan a motorbike to give it the capability of reverse engineering of parts and components.
It will enable the business to test new products and design in a virtual environment, before using 3D printing to produce prototypes quickly and cheaply.
Also, once the vehicle is scanned, the design data is stored and accessible at any point in the future to explore aftermarket opportunities.
The new CAD software will enable Fuel Exhausts to capture vital data to create design specifications and bill of materials, as well as aid new product development, and produce graphics such as 3D exploded views for assembly and build instructions.
The investment will also create two new production operative jobs.
The vision for Fuel Exhausts is to be able to invest in a new digital machining centre to be capable of making the parts themselves, rather than relying on external suppliers.
Damian said: “We are a small business with a big reputation for great work. It has taken a lot of hard work to get to this point and we see digital tools and technology as a way of making our processes much more efficient. This is a first, but major step.”