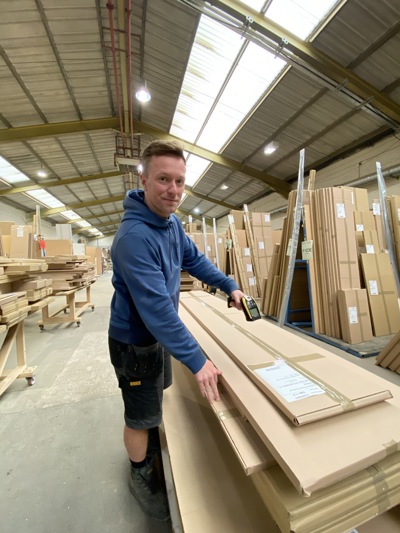
Integral Surface Design (ISD) is embedding a digital IT infrastructure in its new warehouse and logistics centre in Burscough, linking it up to its headquarters and manufacturing hub in Skelmersdale.
The solution includes a new barcode system and upgrading its ERP system’s software to give the business complete visibility of all operations in real-time and enable the warehouse to be managed remotely.
The investment supports the business’s bid to enter a new market selling additional ranges of doors, but will also lay the groundwork for a more agile response to new opportunities.
View the case studyThe furniture and fittings industries face unique challenges in a fiercely competitive global market, where there are ever increasing demands for a greater range and complexity of products and services.
We have identified an opportunity to enter a new market and, with the help of Made Smarter, have put data and systems integration at the heart of that solution.
Dave Hourigan, Digital Transformation Manager of Integral Surface Design
Launched in 2012 ISD has grown over 10% year-on-year to achieve a turnover of £8m, employing a team of 85 people at its manufacturing hub which specialises in made-to-measure PVC foil wrapped doors and furniture components. Now, intense competition has driven the business to embark on a digital transformation.
The first stage, to link all its business operations, including sales, manufacturing and accounts through a custom made ERP system, has reaped rewards in terms of identifying efficiencies and reducing costs.
This data-driven approach has given ISD the confidence to explore a new market which requires building a new warehouse facility.
The aim is to embed a digital infrastructure that connects it with the manufacturing hub six miles away, giving the business full remote visibility of its operations, increased traceability, and opportunities for data analysis.
New IT infrastructure will link ISD’s supply chain, warehouse, manufacturing, logistics, and accounts operations.
The project will also update the software on its ERP system to give the business complete visibility of all aspects of operations in real-time and enable the warehouse to be managed remotely.
Central to stock visibility is a barcode system which enables ISD to verify and monitor stock from when an order is placed, all the way through to delivery.
Delivery drivers will also use barcode scanners to register when the products reach their destination, updating the system automatically.
By digitalising workflow, previously paper-based and time consuming jobs are eliminated, increasing the productivity of the entire workforce.
From warehouse operatives and delivery drivers and their optimised picking and delivery routes, to the sales team who will spend less time looking for information and spend more time nurturing current customers and developing new opportunities.
Real time data and live visibility will eliminate the need for time consuming physical stock checks.
Remote oversight and automation will enable the leadership team to better manage resources and focus their time on more high value activities.
Lean warehouse management will also enable ISD to offer customers a faster turnaround of goods and deliver OTIF, whilst maintaining minimum stock levels. This will increase available funds to invest in future manufacturing expansion rather than being tied up in excess stock.
By using data analysis ISD will be able to pursue a programme of continuous improvement, identifying opportunities for incremental gains through efficiencies.
ISD has already seen the benefits of a more sustainable approach to its business operations. Instead of transporting the 20 tons of production waste material from the site a week, it now uses the material to heat its factory at Skelmersdale.
Connecting the two sites digitally will all but eliminate the need for inter-site travel, while optimised logistics and delivery operations ISD forecasts are forecast to reduce mileage and fuel costs by 10%.
Meanwhile, data analysis and AI tools will enable the business to monitor industry trends and help the business be more responsive to fashion trends.
ISD’s ambition is for a smart factory which optimises technology from design to production to delivery.
“By making the changes that we have already undertaken within our organisation, we recognise that digitalisation is a must and without it future growth becomes very difficult,” Dave explained.
“Made Smarter’s support has been brilliant. It has driven that digital element and enabled us to stay ahead of the game.”