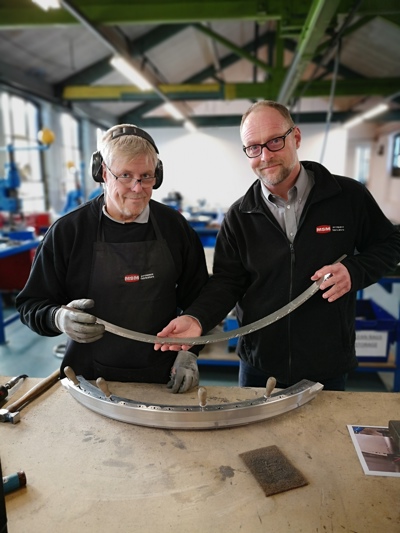
A Manchester aerospace manufacturer has invested in Digital Twin technology to redesign its new factory and unlock production and capacity planning in the future, thanks to Made Smarter funding.
Designing, developing and delivering parts for Airbus and Boeing, MSM aerospace fabricators and its 60-strong team has outgrown its current premises and is planning a new state-of-the art factory. Cutting-edge Digital Twin technology will enable the business to optimise the design and layout of the factory floor prior to build by generating a digital replica of the plant.
Made Smarter has supported MSM to broaden the scope of the project to be able to simulate individual production processes to identify, streamline and maximise operational efficiencies. This pairing of the virtual and physical worlds will give MSM never-before-seen analysis of data and monitoring of systems to manage problems before they even occur, prevent downtime, and even plan for the future by using simulations.
Case Study - MSM Aerospace FabricatorsThe technology will accelerate the business’s growth. The honest truth is that without Made Smarter funding we wouldn’t have committed to such an advanced level of simulation. Our plan was always focused on design as a discrete project. This extra investment means we get maximum value from the technology in the future. It also means that we could do it immediately rather than delaying – propelling us forward by years.
Michael Pedley, Managing Director of MSM aerospace fabricators
During its 80-year history, MSM’s growth has meant expanding its footprint at its site at Spring Vale Works in Middleton. The proposed 35,000 sq ft factory on adjacent land offers a golden opportunity to rethink its manufacturing processes.
Michael explained: “We are growing at a quick rate, and we’ve run out of space. This is an old mill building which has been extended where possible, but its layout is configured to each of our processes – press shop, welding area, laser unit, etc. Some of our more complex assemblies therefore move around the factory numerous times. On a recent value stream mapping exercise, we found that one item travels two miles during its manufacture. That’s staggering. Moving to a single level factory enables us to change layout to be flow orientated and design the most streamlined manufacturing process possible.”
MSM has invested in a Siemens Digital Twin software to create a virtual reality simulation of its current and proposed facilities. This allows the business to model product flow through its manufacturing processes in order to establish the most efficient layout without costly mistakes or delaying production.
Michael said: “We have five presses and the heaviest is 80 tonnes. When we move, that press will need to be installed in a pit and piled. It needs to be located in the correct position for both current and future product lines. We must get it right first time.”
Being able to create a live operational virtual Digital Twin of its factory will enable MSM to test ‘what if’
scenarios to further optimise its production processes.
“Traditionally if the customer doubled the production rate there would be five people standing around a whiteboard brainstorming the impact of that. With the Digital Twin this means one engineer at a computer inputting some data and pressing ‘go’ and to get the result instantly.”
Its new factory is a major commitment for MSM, so being able to eliminate unknowns and mistakes will ensure the whole process runs smoothly. The ability to simulate and then create the most efficient layout will reduce product movement, relieve bottlenecks, improve flowline production and ultimately be quicker to market. The cumulative effect of these improvements is that MSM will become more productive. MSM predicts a growth rate up to 20% a year, allowing it to break the £10M turnover mark in the next three years, which could bring a £401,000 boost to the region’s GVA.
New jobs are expected to be created over the next three years, but Michael has a laser-focus on the next generation of engineers.
“While many of our staff have been trained in traditional aircraft fabrication, the employees MSM needs for the future will also have digital skills,” he said “Part of our strategy with the new factory and the simulation technology is to make skills development a real focus.”
Being able to simulate outcomes will give MSM confidence to make future strategic plans before investing in capital equipment or infrastructure to meet the demands of the business.
Michael is already looking at other advanced manufacturing technologies including robotic welding and enrolling staff onto Industry 4.0 leadership courses.
“MSM has an 80-year heritage in this industry, we are a growing, forward-thinking, digitally compliant SME,” he said. “This investment puts us at the leading edge of advanced technologies and in a great position for the future.”