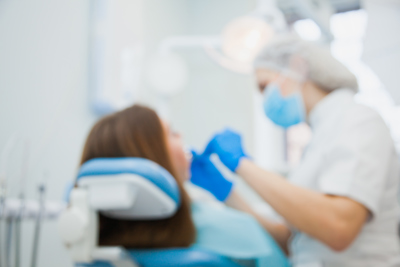
An innovative dental laboratory, supported by Made Smarter, is adopting digital manufacturing processes to create faster and safer treatment for patients, and drive innovation in its sector.
Sandstone Wirral, based in Heswall, are investing in technology and digital tools to overcome capacity restrictions from infection control measures caused by Covid-19, which threaten the viability of the business.
So far co-owners Prof Fadi Jarad and Dr Kate Blundell have invested in a cloud-based patient management system and 3D X-ray technology which minimises patient contact with the surgery.
They are now introducing a digital intraoral 3D scanner, design software, and 3D printing technology in order to create digital impressions of patients’ teeth.
This will enhance non-contact impression taking and enable the clinic to manufacture medical devices such as temporary crowns or dental prostheses in-house.
The new capability will streamline the process, improve the speed and accuracy of treatment, enhance patient experience, reduce paper use and waste, and increase the company’s profitability.
Prof Jarad said: “The pandemic had a significant impact on the practice, closing us down for three months, and then running at 50% capacity to abide by social distancing and infection control guidelines.
“In order to reopen and recover to pre-Covid levels we have had to innovate, redesigning our clinic to create a safe and efficient working environment for both staff and patients by reducing the risk of viral infection spread and optimising chair time.
View the case studyWorking with Made Smarter has given us the know-how and the confidence to take steps to transform our practice into a digitally-oriented centre of excellence, which will significantly increase the potential for post lockdown recovery and growth.
Professor Jarad, Co-owner of Sandstone Wirral
While Sandstone was closed during the 2020 lockdown, and anticipating the safety measures needed to reopen, the business conducted a root and branch analysis of its operation.
It identified an opportunity to create a contactless patient journey and move away from conventional physical impression techniques which are used when fabricating medical devices such as crowns, bridges, implants and dentures.
Dr Kate Blundell explained: “Taking an impression involves mixing material which is loaded into a tray, then inserted into the patient’s mouth until the material is set. This can take several minutes and can be uncomfortable for patients and induce retching and/or coughing which results in the production of aerosol particles which is a health risk in the current climate.”
“The process then involves the teeth model being transported to a laboratory for manufacture into a bespoke medical device, which can take up to three weeks. Sometimes additional patient visits are needed if there is a problem at the fitting stage, and on rare occasions errors can result in the entire process having to be repeated. This impacts on patients and results in lost or wasted surgery time for the clinicians and the business.”
Sandstone’s digital workflow project will introduce digital intraoral scanning, the associated CAD CAM software, and a 3D printer.
Intra-oral scans of a patient’s teeth will enable the clinic to acquire and visualise in 3D the patient's unique anatomy. This digital STL file will be added to dental records stored on the cloud and therefore be accessible to the whole dental team.
The dental team will also be able to show patients visual representations and simulations of the treatment.
A 3D printer will enable the clinic to use the digital records to design and manufacture various medical devices such as temporary crowns, impression trays, stents, study models and splints.
A cloud-based platform means patient dental records will be accessible to the whole team simultaneously, therefore increasing the efficiency of the treatment process and improving patient care.
Using a digital impression technique will eliminate the aerosol generated, reducing the safety risk, while improving the efficiency and comfort of the impression making process.
The dental team will be able to show visual representations and simulations of the treatment digitally and increase patient acceptability for treatment and reduce potential anxiety.
The digital scanner will reduce the impression process by around 50% from 15-30 minutes to just a few minutes, making the procedure significantly more efficient.
By decreasing treatment time, Sandstone estimates that it will be able to increase capacity by 25% from its current 50% covid-reduced level.
Whereas analogue impressions require a dentist, digital scanning can be done by trained nurses. This will upskill the workforce and free capacity for the dentist to provide care for more patients requiring higher value treatments.
The new process will eliminate the use of impression materials and models, which currently accounts for 15% of the total waste produced by the practice, reducing costs and increasing profit.
The digital scanner element is forecast to enable 33% growth in revenue the first year and up to 107% over five years.
Once the in-house manufacturing phase is implemented the costs of laboratory manufacture will be eliminated and waiting time of up to three weeks will be reduced to one week, potentially improving to three days as staff are trained and practiced.
Savings from the entire digital workflow are forecast to increase Sandstone’s profit margin by 14%.
Prof Fadi said: “Our investment in technology will establish a faster, more accurate manufacturing process, which will simultaneously improve patient care and satisfaction by reducing time between appointments for patients, the length of them, and the frequency.”
Sandstone plans to capitalise on this increase in capacity by investing in upskilling staff through training and investing in the expansion and growth of the business by increasing working hours and creating two new jobs over the next three years.
The new digital process which transfers impressions electronically to laboratories for manufacture instead of physically delivering or picking them up, will also significantly reduce Sandstone’s carbon footprint by saving three round trips per week, the equivalent to 361,944g CO2 over a year.
Sandstone’s ambition is to develop and refine the process while expanding its manufacturing ability to be able to perform a full treatment for a patient in one visit.
By developing and implementing an efficient and cost-effective digital acquisition and additive manufacturing system the business wants to establish itself as a ‘centre of excellence’ for the region, that can be used as best practice to other dental practices.
Dr Kate said: “Working with Made Smarter we will set ourselves apart from the competition and showcase ourselves as an innovator in the sector.
“This project will have an overall positive impact on the national, and potentially global dental sector, as innovations provide a safe working environment during and after the pandemic.”