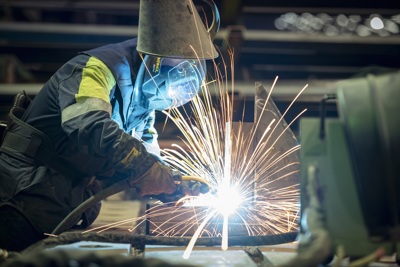
Sheffield Forgemasters, a manufacturer specialising in the production of casting and forging solutions for the world’s most complex engineering challenges, collaborated with MESTEC, a technology company which works with manufacturers to improve productivity and performance.
Operators now use touch screens to report the
status of a production job. This real-time shop floor data is collected, collated, analysed, and automatically updates a set of company-wide KPIs which are displayed around the factory to enable operators and managers to monitor performance.
Dr Megan Ronayne, Head of Industrial Technologies and Manufacturing, Innovate UK KTNMESTEC’s partnership with Sheffield Forgemasters is a tremendous example of the transformation through collaboration that can be achieved using digital technology, and precisely what the Made Smarter Innovation Network
is aiming to replicate over the next four years in its role of joining communities together to drive positive change and transform UK manufacturing.
Although one of Britain’s oldest engineering companies, tracing its history back more than 250 years, Sheffield Forgemasters has remained competitive through innovation and embracing change.
While the Sheffield-based business has invested in state-of-the-art equipment, it was predominantly reliant on paper- based and manual reporting processes for its manufacturing throughput. This meant productivity and costs were only known after the job was completed.
Meanwhile, different departments were measuring performance via different methods.
Rob Woodhouse, Master Production Scheduler at Sheffield Forgemasters, said: “Using handwritten cards was
a legacy system which needed overhauling. The lack of oversight that the system offered, meant that we had to assume performance, efficiency and Overall Equipment Effectiveness (OEE), and there was delayed visibility of costs.
“We understood that significant change was needed to support customer requirements and ensure deadline deliveries, and that finding a technology solution would also help us understand our capacity to enhance scheduling, increase productivity and increase profitability.”
Sheffield Forgemasters began working with Bracknell-based MESTEC which conducted a root and branch analysis of the production processes and systems.
MESTEC was then able to configure its off-the-shelf MES (Manufacturing Execution System) software to model Sheffield Forgemasters’ processes, linking shop floor production, digital production management systems and planning software into a cloud-based data collection platform.
Mark Carleton, CEO of Mestec, said:
“By digitising its whole manufacturing lifecycle we created a solution which mapped out the best practice for its processes and accurate times for its production. We could then import its current workflow to enable advanced planning and scheduling capabilities. By upgrading its data and systems infrastructure to enable scalable expansion we enabled real-time accurate shop floor data collection and analysis to make performance transparent and allow the business to drive continuous improvement.”
By eliminating spreadsheets, paper- based operations and manual data collection, and replacing them
with automated shop-floor data collection, dynamic production planning, and real-time performance analytics, Sheffield Forgemasters has significantly improved its manufacturing processes.
The new system means data collection is efficient, accurate and automated, enabling real-time visibility of the entire factory - a transformational change from data collection processes of the past.
Supervisors are able to see more clearly what’s happening on the shop floor and react in a timely manner
to reduce operator or machine downtime, increase productivity, and reduce waste.
The new system means that Sheffield Forgemasters can better manage time, process, costing, and information flow to customers.
In the office, the costs of managing paper and spreadsheets has
been reduced by 40% with a 20% improvement seen in planning efficiency.
The company’s most recent customer assessment demonstrated significant improvements and is approaching class-leading.
The digital transformation has also resulted in new skills flooding the factory floor, with training and job development for many of its 650 staff.
Rob Woodhouse added: “The solution has given us a visibility that simply wasn’t there before, a site-wide start to finish view of our processes, enabled data-based decision making and new levels of manufacturing intelligence.”