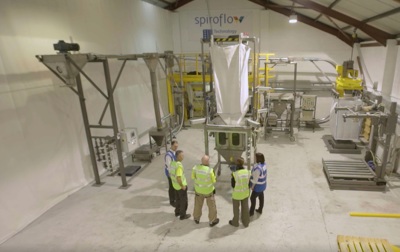
Process equipment manufacturer using Industrial Internet of Things (IIoT) demonstrator to drive digitalisation in sector.
A powder and bulk solids equipment manufacturer is driving digitalisation in its sector with the Industrial Internet of Things (IIoT), through the support of Made Smarter.
Spiroflow, based in Clitheroe, has developed a remote monitoring system that provides real-time information on the performance of its complete machinery range.
Spiroflow Active Monitoring (SAM) automatically monitors customers’ equipment through sensor-based technology. It provides key performance and operational insights through a dashboard which can be reviewed in real-time on PCs, tablets, smartphones, and smart watches from anywhere in the world.
Made Smarter has provided digital strategic advice and support to allow Spiroflow to transform its own factory into a showcase to demonstrate SAM’s capabilities to the sector.
View the Case StudyOur vision is to transform the powder handling industry through the adoption of digital technology. This is about changing mindsets. By implementing the technology into our own plant we will be able to educate customers and the wider industry about the benefits and capabilities of IIoT and data.
Support from Made Smarter has allowed us to be more ambitious in the scope of our demonstrator to develop the technology faster and accelerate the route to market.
Craig Hollings, Technical Development Manager of Spiroflow
Over the last 50 years Spiroflow has become a global leader in the manufacture of bulk materials handling and powder processing equipment.
In its efforts to constantly innovate, the business has upgraded its machinery to include more automation solutions, sensor technology and IIoT.
Spiroflow has seen the opportunity to add value by offering data and analytics services.
“IIoT has enormous potential for manufacturing,” Craig said. “Our blue chip customers are used to having data fed back to them and using advanced technologies like AI. But many of the SME producers just aren’t at that level yet. While some may still be using pen and paper to capture data and make their own calculations. We want to change that approach and show them what is possible, both with our equipment, custom control panels, and standalone factory IIoT solutions.”
SAM’s goal is to collate key performance indicators from sensor data and compare it with digital and historical analytics.
Built into Spiroflow’s control panels, the technology captures a wealth of relevant data such as the hours that a machine is running, motors operating at higher amps, unusual spikes, issues on site that may cause failure or under-performing parts.
The system is capable of collecting and analysing the data from one machine to the entire facility, transmitting it for display on a dashboard.
Craig said: “With SAM you will get faster and better-informed decision making by unlocking critical data about equipment performance and putting the facts into the right hands. It will pinpoint any system bottlenecking and wasting production “up time” giving you the capability to see the system, but also being modular, it will allow you to further streamline your process for lean manufacture.
“SAM will allow our customers to have unbiased facts at their fingertips allowing for an enhanced overview of equipment performance, together with the ability to quickly identify issues and rectify them. Clearly by having the means to implement precise measures, a catastrophic equipment failure and resulting downtime can be avoided.
“By turning our plant into a Smart factory we are practicing what we preach. We want to be able to show how we have implemented SAM and to educate our customers to these benefits by specifically monitoring their equipment.”
The benefits of SAM go beyond Spiroflow and its customers to the sector as a whole.
For its customer it means an operator no longer needs to constantly monitor equipment or processes. Plus there is no manual data collection and analysis, because data is collected, processed, and exceptions reported on a real time basis.
This means customers can be alerted of potential safety hazards before they arise, given constant insight into equipment performance, and be made aware of maintenance schedules to eliminate costly and unnecessary downtime.
By offering SAM as a subscription it enables customers to test the waters of the capability of data and build up its understanding and expertise.
For Spiroflow, remote access to its customers’ equipment means engineers will be able to carry out diagnostics without the need to travel, which will significantly reduce travel time, cost, and emissions, and make its maintenance and repair service more efficient and productive.
Access to the data will also give Spiroflow insight into the predictive maintenance of its equipment., meaning it can stock the right spare parts and become more efficient.
The data will also help Spiroflow understand its product range better and provide feedback into its research and design process.
The demonstrator will allow the business to show and tell customers and the wider industry what is possible.
Craig said: “We want to take our customers’ mind away from the basic machine, the motor and the sensors, and show the bigger picture on the dashboard where all that data is captured and displayed.
“For example, we want to demonstrate how oxygen levels, dust particles, humidity, light and temperature all impact process and operation, and how they can affect the bottom line.
“We are trying to illustrate the gains they could make in real-time and in the longer term.
“Of course we want to sell more equipment solutions, but we also want to expand what we offer customers and secure long term partnerships. This is very much about raising awareness of the benefits of digitalisation and bringing them along on the journey towards Industry 4.0.”
Ultimately, Spiroflow wants to monitor, not just its own equipment, but any equipment both with our control panels, and stand alone IIoT sensors.
“Our vision is to transform the powder handling industry through the adoption of digital technology,” Craig said. “By supporting our project, Made Smarter is not just helping us, but helping many others adapt to new technology.”