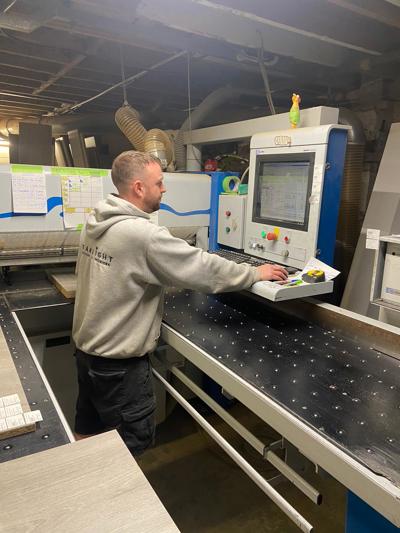
A furniture manufacturer, supported by Made Smarter, has invested in a game-changing technology solution which is forecast to increase productivity by 15%, create new jobs, and unlock growth potential.
Starlight Bedrooms, based in Bolton, is creating a bespoke Customer Management System which will integrate with new CAD design and production software, and its sales and marketing operations.
By capturing vital data and connecting key systems, the company will streamline its processes, remove bottlenecks, reduce errors and waste, and become more efficient, productive and profitable.
The new system puts improving customer experience at the heart of its plans, reducing the design and quoting process, from a week to just one day.
Working with Made Smarter has been incredibly valuable. The experience of creating a digital transformation roadmap and the subsequent support and expertise has given us a lot of confidence to invest in the tools and technology we need to take Starlight Bedrooms to the next level.
Karen Callard, CEO of Starlight Bedrooms
Starlight Bedrooms was taken over by Karen and three other family members in 2018 when its founder retired.
While the business, which has 17 staff, had a good foundation in terms of machinery and a strong reputation in the marketplace, it lacked digitalisation across its operations.
Through Made Smarter’s digital transformation workshop- a fast and fully-funded diagnostic of the business’s product, services, processes and people - Starlight identified key challenges and opportunities, including: establishing data and systems integration, improving its design and ordering process; and optimising part of its production process.
“Our biggest challenge is our outdated, manual and paper-based processes, and a lack of digital connectivity between any of our business operations,” Karen explained. “Nothing talks to each other, processes are unnecessarily onerous, time consuming and inefficient, and expose us to error.”
“For instance our design and ordering process takes anything up to a week, starting with a designer taking measurements manually and talking to a customer about their specific desires for the room, drawing a plan and passing it on to someone else to create a 2D CAD drawing which is then manually priced and posted to the customer.”
Starlight has also identified the manual process of ordering materials from suppliers, often done by fax or telephone, is open to error and lacks traceability. The company also has limited visibility of its stock.
“We made some big changes, making social media central to our marketing strategy and saw some instant success,” Karen said. “But we recognised that to really grow the business we needed to tackle productivity challenges, improve our overall efficiency and reduce waste behind the scenes, while improving our customer experience.”
Starlight has embarked on a project to create an integrated Customer Management System which will allow everyone full visibility of the complete sales and production pipeline and which will require all sales and production staff to utilise the system.
Data from site surveys can be used to rapidly generate room layouts and furniture and fittings configurations in a new CAD system.
These configurations are linked into a costing, materials and workflow planning and management module. A data link will send machine instructions to Starlight’s production plant and this will be merged into its materials utilisation package.
Real time data will be available for planning and progress to ensure clients and fitters are informed of the correct installation date.
Starlight is also aiming to improve production processes by investing in staff training in Woodwop, a CNC program system, and Magi-Cut, a software system to optimise panel cutting.
Longer term plans include exploring direct links with suppliers to improve ordering efficiency.
Automation of time-consuming tasks will free up key members of the workforce to refocus their skills on areas that can drive the business forward.
It is anticipated the project will increase productivity by 15% and significantly improve the communication process with customers.
It will support the business to increase production from 10 rooms per week to 15.
The forecast increase in business, resulting from the improved systems, is expected to create up to nine new jobs.
Current and new staff are being upskilled in the new CAD system and the designer is being provided with a tablet computer so that technical drawings can be uploaded the minute they leave the customer’s home.
An automated pricing system will speed up and increase the capacity to provide quotes and estimates, and allow the Operations Director to focus on more essential areas of the business.
The company is forecast to reduce waste across its operations. New production software will ensure more accurate cutting and less wood waste, while improved stock control will enable better oversight and control over resources.
By improving the customer experience, Starlight forecasts that it can increase sales by 20% and increase turnover accordingly.
Karen said. “We operate in a congested market, so we need to set ourselves apart from our competition. This investment puts the customer at the heart of the business and allows us to build on our USPs.
“This project will also allow us to get control of the valuable data within our operations and give us the foundations to make insightful decisions for future growth.”
Demand for home improvements during the pandemic has resulted in a surge of orders for Starlight, giving Karen and the team great confidence for the future.
The next stage of growth for Starlight is to improve its capacity by investing in larger premises.
There are also plans to enhance the customer experience by providing real time updates about the production of customer’s furniture. The organisation plans on utilising large screens at its two showrooms to demonstrate designs and use tablets or interactive computers to show alternative colours, textures and finish options to the customer there and then.”