Materials need to be converted from raw form to a usable prototype when developing an innovative new manufactured product. It is often not possible to re-use that material so unless the product is a success, that material and the engineering time spent developing it is wasted. Moreover, developing a successful physical product often requires multiple iterations to achieve a successful prototype; all of the failed attempts amount to wasted time and materials. With digital innovation and the use of agile methodologies, conversely, there is no wasted material that has had to be acquired: the code just needs to be tweaked and re-worked. As Nick points out in the episode, this reality means that a lot of research has to take place before a research engineer begins working on a manufacturing technology innovation. This is very different compared to digital innovation where rough prototypes can be run up in days if not weeks. As is discussed more below, rough prototypes can be enough to prove out a digital concept and the code base can also be incorporated in the mature solution. There are other reasons why innovation in digital technology is less risky, more affordable and even sustainable then innovation regarding manufacturing technology as we discuss in the podcast.
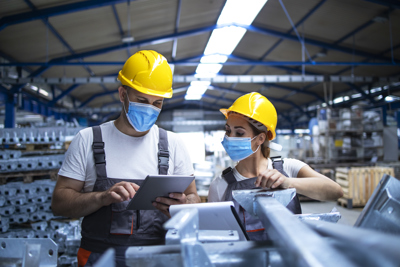
While much has been written about the devastating costs brought about by COVID-19 both in lives and to the global economy, in the world of manufacturing, there are likely to be some silver linings that will bring about a revolutionary change to the sector.
As Dr Nick Wright and I discussed on the premiere episode of the new podcast series, Time for ChAI, one thing is undeniable: people need to start thinking about what the world of tomorrow might look like, for the world of tomorrow will not look the same as it does today. This is particularly true in manufacturing.
As the manufacturing industry shifts from ‘firefighting’ mode to acclimatisation, one of the key areas of manufacturing that has received significant attention due to the COVID-19 outbreak is supply chain resilience. As Nick highlighted in the opening exchange of our conversation, COVID-19 brought about massive downturns in demand in sectors such as automotive and significant shortages of supply in other sectors such as food and drink and consumer goods (for more on FMCG supply chains listen to this episode).
Instances such as the latter present opportunities to those who are able to respond fastest to rapid, overnight increases in demand; while scenarios akin to the former, highlight the necessity of pre-emption. Businesses that come out on top will be the ones that were able to reduce their exposure to market volatility before the rest of the sector had even registered the magnitude of the threat. In both cases, digital technology can be an enabler, as both ChAI and Digital Catapult know all too well.
As Nick highlights in the episode, the widespread adoption of digital technology will only take place if there is a widespread shift in attitudes to innovation.
Key to this shift in attitude is partnerships. However, as Nick points out in the episode, not the one-sided kinds where the agenda of a so-called ‘partner’ does not align with that of the manufacturer and is in fact just looking to extract resources. The widespread adoption of digital technology in manufacturing is not akin to the adoption of the enterprise resource planning system, bought off the shelf from transactional vendors. It is about true partnerships where complimentary parties share expertise, risk and reward. Unlike efforts to optimise manufacturing technologies, efforts to adopt new innovative digital technologies are not zero-sum games. In this instance, all ships rise together with the tide.
A common argument to the points prescribed here, or indeed those discussed in the episode itself, may be that changing attitudes to digital technologies or experimenting with innovation are not feasible if you are an SME. In response, I would encourage you to listen to the episode and hear the examples cited of businesses who have adopted digital technologies where there was a clear business case and they had a partner to work with them through the process.
Organisations such as Digital Catapult, High Value Manufacturing Catapult, the MTC and the MTA understand very well the perspective of manufacturers and, generally, have agendas that are complementary. They know how to bridge the gap between manufacturers and digital-native businesses such as ChAI who do something very specific that yields quantifiable business value and revolutionary results.
The moment of introspection brought about by COVID-19 is as good a moment as any to think about how you can leverage innovations facilitated by digital technology in your business. It's undeniable that those that do so, with prudence and purpose, will not just survive, but thrive in a post-virus world.
ChAI is democratising access to commodities price predictions in order to help manufacturers reduce their significant exposure to commodity price volatility.